Choosing Lines For BASE
Dacron, Spectra, or Vectran: Breaking it Down
Choosing which lines you need on your BASE canopy is actually a very simple process, so if you don’t want to read a long article, here you go: If your BASE canopy will be used almost exclusively for jumping slider up, and you want to minimize weight and bulk, then choose Spectra. For almost any other scenario, Dacron is the answer.
So what else is there to say? And what about Vectran? For those of you who want to know the background on this simple advice, or are curious about what these words mean, here are a few more details on each line’s properties.
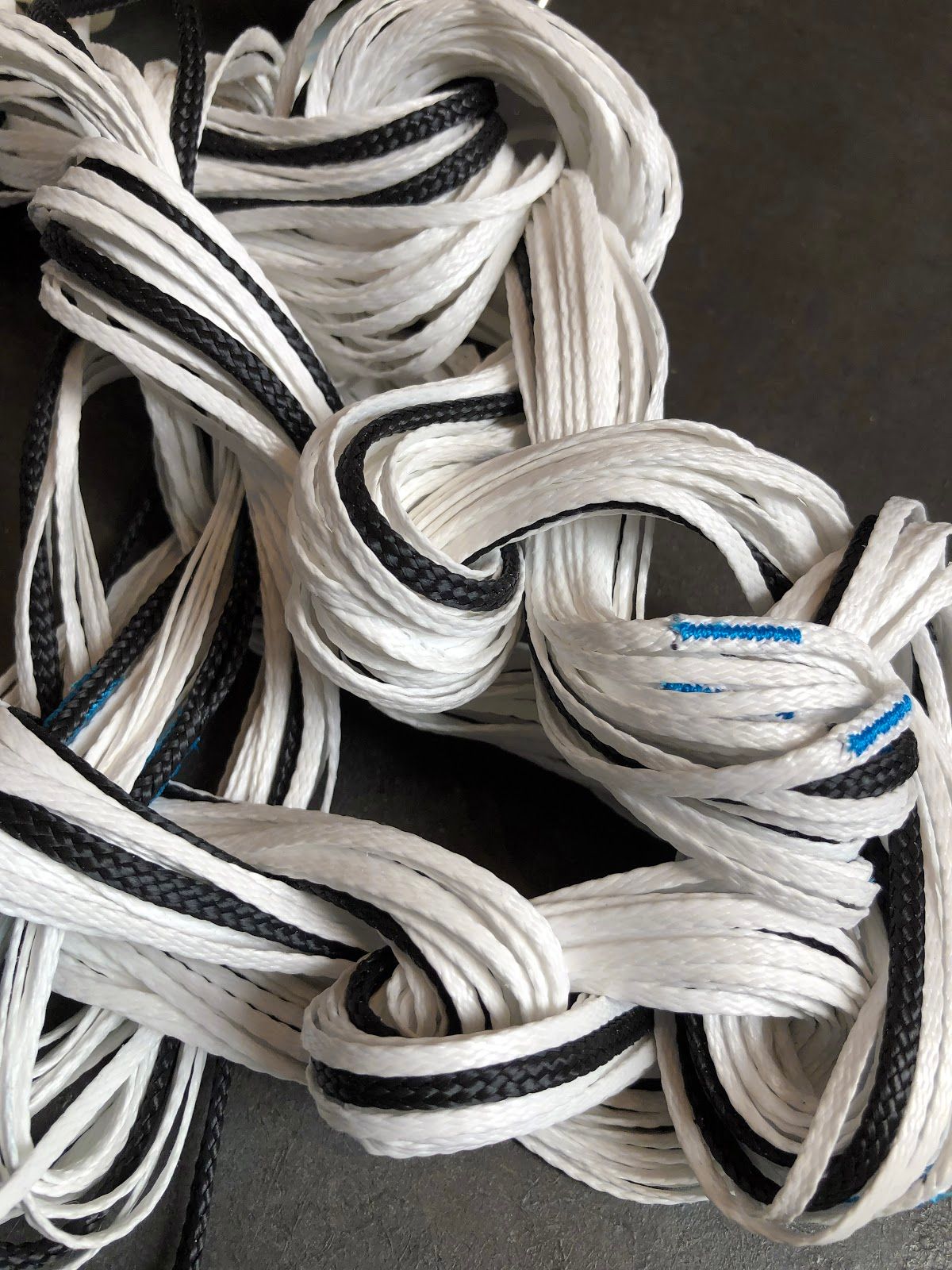
SPECTRA (™ of Honeywell) & DYNEEMA (™ of DSM)
Both are: Ultra-High Molecular Weight Polyethylene, or UHMwPE.
Spectra is a trademark name of a yarn product manufactured by Honeywell in the USA. It is molecularly identical to Dyneema, which is manufactured by DSM. This material is pretty cool stuff, and it’s worth learning about it. The Epicene is made with Spectra, and this line is an option for Hayduke as well.
Spectra has some unique characteristics that make it especially well suited for use in certain parachute designs. It is strong, light, doesn’t absorb much water, and has good UV resistance. It ages well, with minimal “furring” and is dimensionally stable enough for low performance parachutes (which describes every BASE canopy ever made).
Here's why we love it for BASE canopies:
- It’s light, and low pack volume, making a significant difference in total weight and pack volume compared to Dacron lines. The upside here is obvious – every gram counts on a four hour hike, and every cubic inch of volume matters when you’re dragging your container through the air at 150 mph.
- It starts smooth, and stays smooth over time as it ages. Compared to Vectran, which becomes a hairy mess as it ages, Spectra stays smoother for longer. This is a positive for tension knots, which become more likely as friction increases between line loops during deployment. Smoother lines make for smoother line deployments.
- It doesn’t absorb much water. When you land your parachute in wet grass on that first jump of the day, and go to re-pack it, you don’t want to be s-folding soggy lines into your tail pocket – especially if they’re nice and hairy after a season of use. Vectran, by comparison, absorbs enough water to where damp hairy lines can be an issue after landing in wet grass.
- Performance. There is a noticeable difference in the glide performance of a Spectra lined canopy vs Dacron. In ram-air canopy flight, line drag is significant enough to affect even low-performance BASE canopies.
Downsides to be aware of:
- Inelasticity. While “less elongation than steel” is a common and inaccurate refrain, Spectra is inelastic compared to Dacron. It is also comparatively low-friction. This can be a bad combination if your equipment is not configured properly, or if you aren’t aware of the conditions you need to provide your parachute in order to have a safe opening. Is this bad? Not if you use Spectra line for its intended purpose, which is for slider up deployments at a controlled airspeed. The downsides of inelastic line material have been the source of many old-school opinions about parachute openings which no longer apply to modern gear. Modern BASE parachute designs are begun from step one with the knowledge that Spectra line will be used. Intentional design features mitigate the drawbacks and now, after more than a decade of use in BASE, the consensus is that Spectra-lined canopies perform well for slider up applications and many wingsuit BASE jumpers swear by Spectra thanks to the benefits. That being said, if we are speaking strictly within the category of openings, Dacron wins.
- Trim. Spectra’s tendency to shrink out of trim is a common complaint, but this argument has limited application to BASE canopies, which are not highly sensitive to the amount of trim loss Spectra tends to experience. The minor downside in trim stability is far outweighed by the benefits of strength and durability Spectra offers. Sidebar: Trim myths*
- Cost. It’s more expensive than Dacron. At SQRL, we do not pass this increase on to our customers.
SPECTRA LINE MANUFACTURING
There is a >90% chance that if you’ve ever seen Spectra (sometimes called “microline”) on a parachute, it was made with Honeywell yarn, by CSR. Here’s how Frank, the owner of CSR, describes the manufacturing process:
“Spectra arrives at our factory from Honeywell in a tube of yarn. We load the yarn into the braiding machine, and begin to braid a line to a specification. First, we braid about six feet of line through the machine, then stop it, and cut the line. That line – the first few braids of every single braider setup every day, is tensile tested before continuing. If, for example, they braid a 1000lb spec line, the tensile test must show a strength of at least 1100lbs in order for production to continue. “We’re not making clothesline”, Frank says, and the QC procedures at CSR are intense. Once approved, the braider will continue to produce around 5,000’ of line over a 20hr period, which accumulates on a supply reel.
From there, the line is taken to another zone in the plant, where Frank’s brother, Tim, oversees the rest of the process. The next step is to pre-tension the line at about 80lbs, in an untreated state. This dimensionally stabilizes the line so that its length remains as consistent as possible through the inevitable load cycles in its future. After stretching, a water-based urethane coating is applied, the excess is squeegeed off, and the line is cured for three days. It’s then put onto another reel, stretched a second time at 80lbs, and rolled onto shipping spools. Before shipping, sections of line are randomly selected for tensile testing a second time.”
Honeywell’s yarn, and CSR’s manufacturing process, are consistent. CSR fails very little yarn, and braided line tests rarely result in failed batches. At Squirrel, we frequently test components built with CSR line, such as soft links and parachute line, and CSR’s rated strength has been exceeded in every scenario.
Interestingly, the lower the line’s elongation, the more the variance is between tests. The higher the elongation, the more consistent it is with a narrower range. For instance, testing five pieces of 1000lb Spectra line may result in failures between 1150 and 1300lbs, but the comparatively elastic Dacron line will usually present a smaller window – more along the lines of 5-8%.
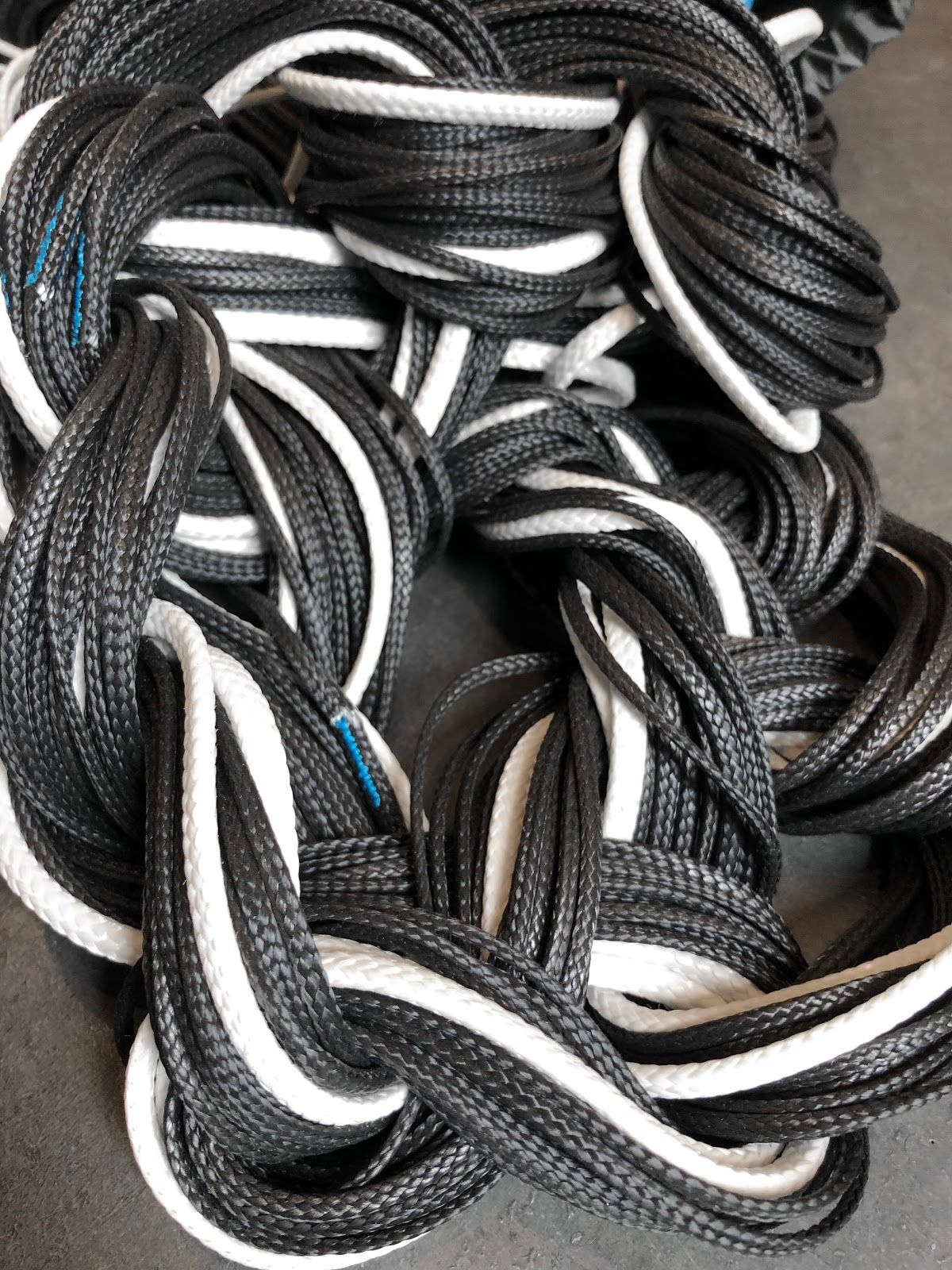
DACRON (Originally ™ of DuPont, now INVISTA N.A.)
It’s Polyester! And BASE jumpers love Polyester.
Polyester at its base, Dacron™ has enjoyed a very long history of use in skydiving. Like flubber, you can beat it up with a parachute opening and it will return to its original shape quite predictably. It is resistant to heat, has a nice amount of elasticity, and is generally easy to use. Dacron molecules are not organized into such long chains as Spectra, meaning that more yarn is needed in each braid to achieve the same strength, therefore pound-for-pound it’s thicker.
Dacron’s elasticity suggests that it is more “forgiving” during the opening process, which can benefit us in several ways. It provides a bit of shock absorption for hard openings. If you’ve ever jumped a Spectra lined-canopy slider off for more than a one-second delay (not recommended), you will understand this difference first-hand, and it’s hardly debatable. So for slider down applications, Dacron is a no-brainer and is currently the best thing going. For slider up openings, its shock-absorbing properties apply equally well. While the staging of the parachute opening by way of slider reefing is the most important factor, a bit of cushion is undoubtedly a benefit.
Upsides:
- It’s Elastic. Softer openings are good when they occur in the same amount of altitude.
- Water resistance. Soggy lines are not a benefit to BASE jumpers, and wet grass landing areas are a daily occurrence for most of us in the Alpine summer. Dacron resists water absorption better than Vectran.
- Good dimensional stability. Not great, but good, and better than Spectra. Overall, this is a minor benefit to BASE canopies which are not severely affected by minor trim changes.
Downsides:
- Heavy, bulky. Pound for pound, Dacron resists less, meaning that we need more material to achieve the same goals. This has consequences for weight and pack volume.
- Not as strong as Spectra, at the same diameter.
- Performance: Spectra is up to 40% smaller in diameter at the same strength, which – even in our low-performance canopies and especially in medium performance canopies – makes for a real difference in glide performance. Line drag is a major factor in parachute efficiency.
VECTRAN ™ of Kuraray
Liquid Crystal Polymer
From the polyester family of materials, Vectran™ is a liquid crystal polymer manufactured in Japan by Kuraray. Vectran can be found on some BASE canopies, but we do not offer it as an option at Squirrel. While we don’t think it is a bad choice, we do think that Spectra is a better choice, achieving similar goals with a more desirable balance between strength, durability, and ease of use. Spectra and Vectran lines are comparable in terms of weight and diameter, but Spectra wears better long term, absorbs less moisture, furs & frays less over time, and is generally more durable (when pitted against UV exposure, bending tests, and even Velcro-abuse, Spectra wins hands-down). Vectran beats Spectra in only one category: dimensional stability (trim).
Upsides
- Trim. Vectran is very dimensionally stable, meaning that it does not have a tendency to shrink or stretch over time. But, this benefit is minimal for BASE canopy use.
Downsides
- Furring. Hairy lines are higher friction. Our position is that smoother is better when lines are paying out of your tail pocket.
- Low UV resistance. This is not a big drawback, but can be significant depending on how the parachute is treated.
- Water absorption. Used Vectran lines can be a bummer when wet. Wet hairy, limp… doesn’t even sound good, does it? Lines in that condition do not deploy smoothly from a tail pocket. The decrease in deployment performance is difficult to measure, but the available evidence is adequate to push us to Spectra.
- Vectran is “brittle” and difficult to inspect. The liquid crystal polymer base that Vectran is made from is a crackly molecule that fails in a spectacularly abrupt fashion, when it does, and the signs of wear are not always obvious.
HMA TECHNORA ™ of Teijin Aramid.
High Modulus Aramid (Para-Aramid)
We get to deal with Teijin and its subsidiaries because we order para-aramid materials and Teijin-Frontier cloth, and have studied aramid-fiber-woven fabrics for our wingsuit applications. Technora is an excellent material with applications far beyond parachute line. It is a co-polymer fiber that is eight times the strength of steel, with excellent heat, UV, and chemical resistance. It’s dimensionally stable, which made it attractive for parachute line applications in the past, but it is no longer as popular as it once seemed it would be in the category of high performance parachutes… again, a category that BASE canopies do not fit into.
TECHNORA has not yet found an application in BASE because it doesn’t seem to provide meaningful benefits compared to Spectra or Vectran, even though, pound-for-pound, it’s smaller in diameter and the elongation properties are not worse than Spectra or Vectran in the category of openings. One significant downside is that it has a reputation for being more fragile than other line types as a result of it being more susceptible to degradation when fibers are exposed to the dirt that BASE jumpers tend to play in.
*DO SLIDER GROMMETS HEAT SHRINK SPECTRA LINES?
In short, no!
It is one of the most common info-nuggets in skydiving: “Microline” (Spectra, or UHMwPE), shrinks over time due to the heat-based friction of the slider grommets traveling down the lines. This is said to be the cause of skydiving parachutes “going out of trim” over time. It is said that the reason the outer lines shrink compared to the more central line groups, is due to the slider friction. Is this conventional wisdom true? Well, not according to the engineers who manufacture this molecule and braid it into cord.
There are two basic facts about UHMwPE line that contradict the conventional “slider grommet heat causes shrinkage” wisdom:
- Spectra stretches when heated & loaded at the same time.
- Braided spectra line slowly shrinks over time on its own, regardless of heat applied, unless it is loaded and re-stretched periodically.
There is one basic fact about parachute openings that contradict the conventional wisdom:
- The amount of heat generated by the slider grommets on the lines is not enough* to affect UHMwPE line, and the heat that is generated is largely contained by the grommet itself.
*According to Honeywell!
Simon Perriard, SQRL’s resident materials expert, says:
“It's not heat, but "less stretching" that causes the length differences across the span of a parachute over time. The effect is minor on BASE parachutes that have relatively hard openings, because during the opening phase you have a more even load spread across the span and chord, and a significant enough load to restretch the entire lineset adequately. It's much more problematic on foot-launched canopies (i.e. Paragliders) because the lack of opening sequence force results in the C and D line groups shrinking significantly more than the more heavily loaded front riser lines (even when we use lines of different diameters in order to size each line proportionally to the load).
Because of the load-unload cycles, line length discrepancies emerge. The effect specific to UHMwPE is called creep deformation, and although the primary phenomenon in the literal sense (shrinking or elongating at the intra-molecular level) is only part of the story, its macro effect makes the braid shrink in significant proportions due to the displacement of the yarns relative to each other when the line is unloaded and manipulated, combined with a slowly increasing inter-yarn friction as the line accumulates dust during its lifespan.”
Simply put, the central lines on your parachute (the ones which, coincidentally, experience what is perceived to be less “friction” on the slider grommets) experience higher loads than the outermost lines on your parachute. They are loaded first, and for longer, during the opening phase. The extra loading “re-stretches” lines in this part of the canopy, while the outer lines are loaded less. The outer lines are seen to be “shrinking” compared to the central line groups, but it is not because of heat - instead, it is due to a lack of constant “re-stretching” that the central lines experience.